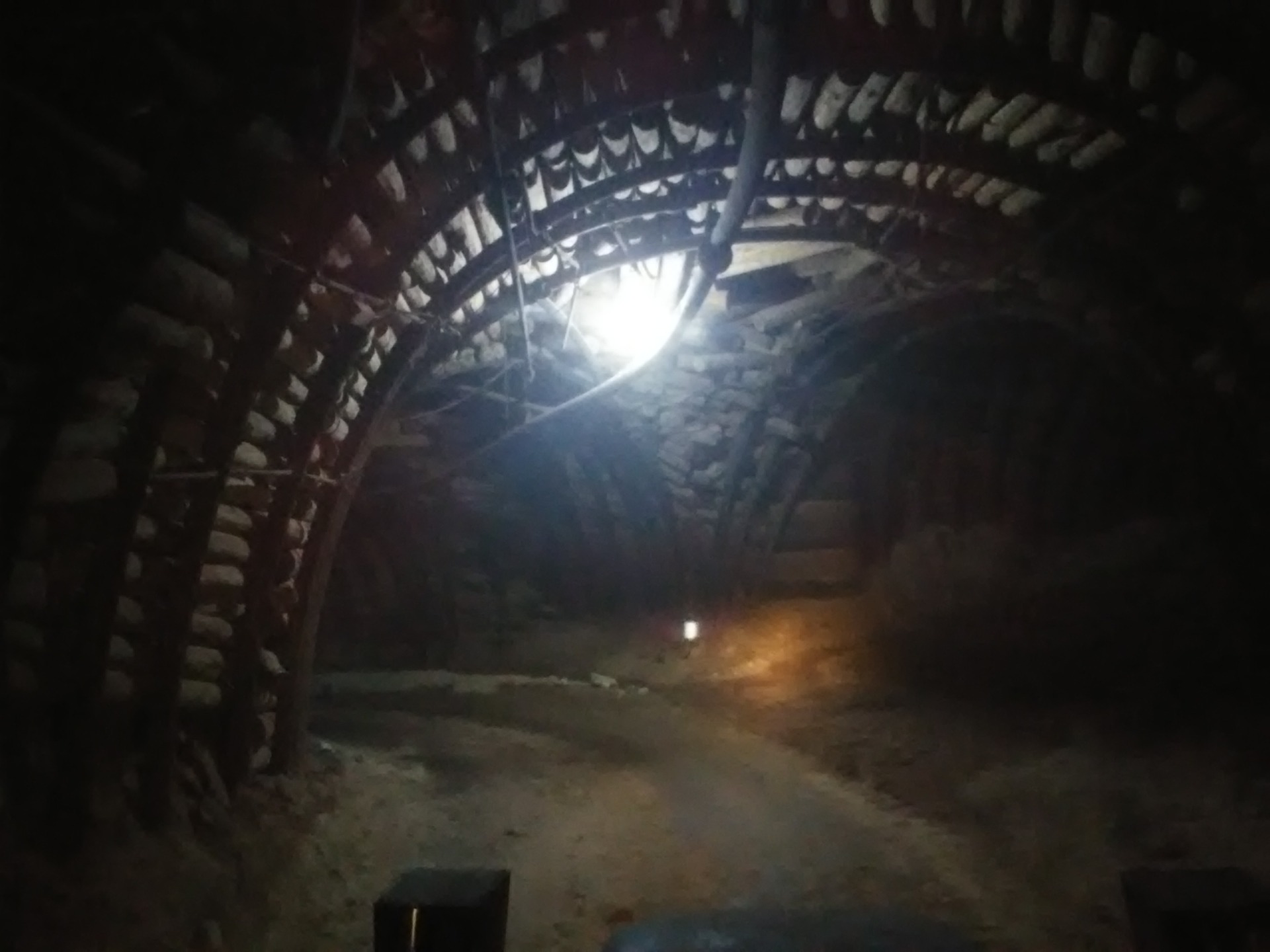
CICLO MINERO
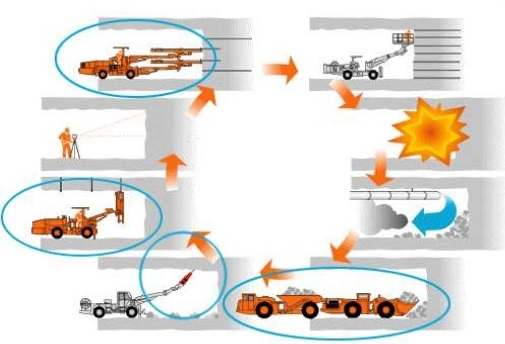
Como mineros, nosotros sabemos que el ciclo productivo no debe fallar, NO debemos tomar atajos en ninguno de los pasos, pues de ello dependerá el éxito en la rentabilidad del proyecto, integridad física de personal y equipo, así como el cumplimiento de metas turno a turno.
El éxito de este ciclo, depende de varios factores, principalmente los "Técnicos", los factores serán mencionados en el análisis de los puntos de este ciclo, encontrados en esta entrada, sin embargo en general, el éxito se debe principalmente a:
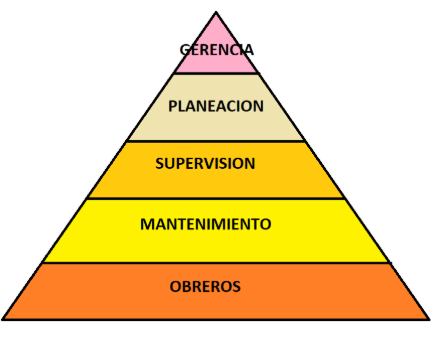
Obreros. - Ellos son la base del ciclo, pues ellos desempeñarán cada una de las acciones operativas manuales y mecánicas en el ciclo, desde los servicios hasta la operación de equipos.
Mantenimiento. - En el segundo orden son los responsables de que los equipos utilizados turno a turno en el laboreo se encuentren en óptimas condiciones.
Supervisores. - Un supervisor con visión y sin mediocridad, desempeña su trabajo de manera activa y pasional, siempre atento a los problemas que surjan en cada una de las áreas de las que esté de encargado en el turno, una buena supervisión minimiza las posibilidades de falla en turno, pues evitará tiempos muertos y entregará calidad de obras..
Planeación. - Tanto geológica, topográfica y de operación, la ingeniería tendrá que marcar un buen rumbo, considerar posibles contratiempos y problemáticas que se presenten y una buena dirección en los turnos desde superficie y aplicado en interior mina.
Gerencia. - La visión de una cabeza con alta competencia se refleja hasta la base de la pirámide jerárquica, pues existiendo gerencia justa y sin favoritismos, se proyecta en los recursos humanos que desempeñarán el laboreo (Desde planeación hasta operación).
El ciclo minero se presenta en manera general en la imagen que se encuentra a continuación:
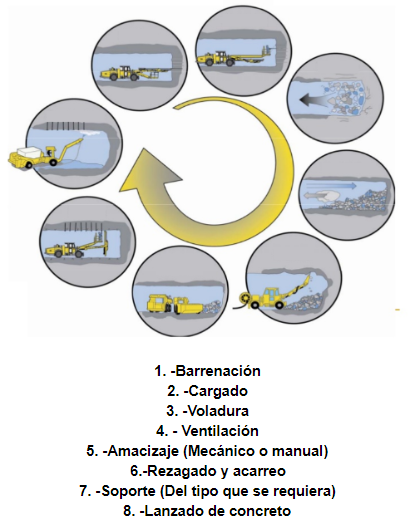
Teniendo mencionados los puntos del ciclo, nos resta el análisis de cada uno de ellos, para lograr una comprensión más clara de la importancia de cada punto.
- Barrenación
El principio de esta actividad unitaria, se basa en la roto-percusión, lo cual significa que mientras "Martilla", la barra tiene rotación, lo cual aunado a la fuerza del avance, va penetrando en la piedra, formando un "Barreno", y gracias a la inyección de agua, se va realizando un "Barrido" del barreno, expulsando la roca triturada.
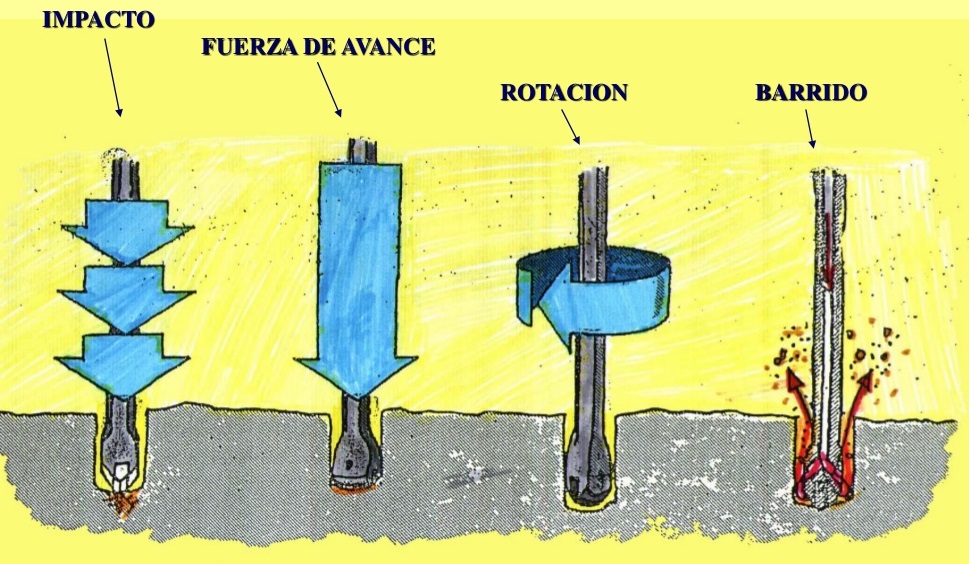
Al igual que cada uno de los puntos de este ciclo, la barrenación es de suma importancia, con un "Plus" agregado, que este paso es el que dará inicio al ciclo y reciclado, este punto es de suma importancia, pues es donde la mayor posibilidad de fallas puede presentarse, por lo cual la supervisión en este punto, debe ser infalible, pues las fallas pueden existir por diversos factores, tales como:
La falta de pericia del operador (Y sin supervisor para corregir los detalles operativos, desemboca en problemas graves para el equipo y/o la operación).
Problemas técnicos (Por lo cual el supervisor debe replantear la actividad en pos de la sucesión exitosa del turno, y evitar el "Tiempo muerto" y mano de obra "Desperdiciada").
Problemas misceláneos como falla de servicios, problemas de aceros, problemas de mal entendimiento de instrucciones, pereza laboral, etc.
Por los posibles problemas como los mencionados (Entre otros), además de tener una visión mas amplia de los trabajos que se realizan, del panorama de las obras, condiciones (Técnicas, seguridad y planeación), es, tal como se menciono previamente, fundamental una supervisión profesional y ética.
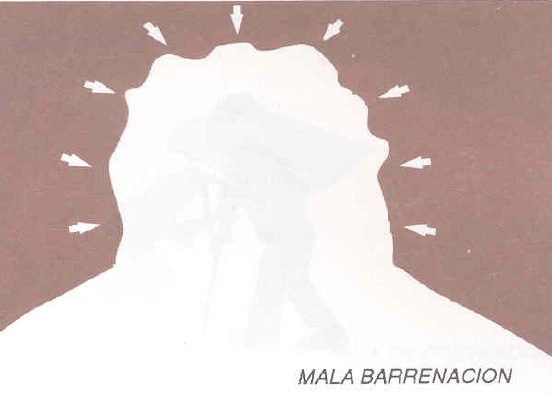
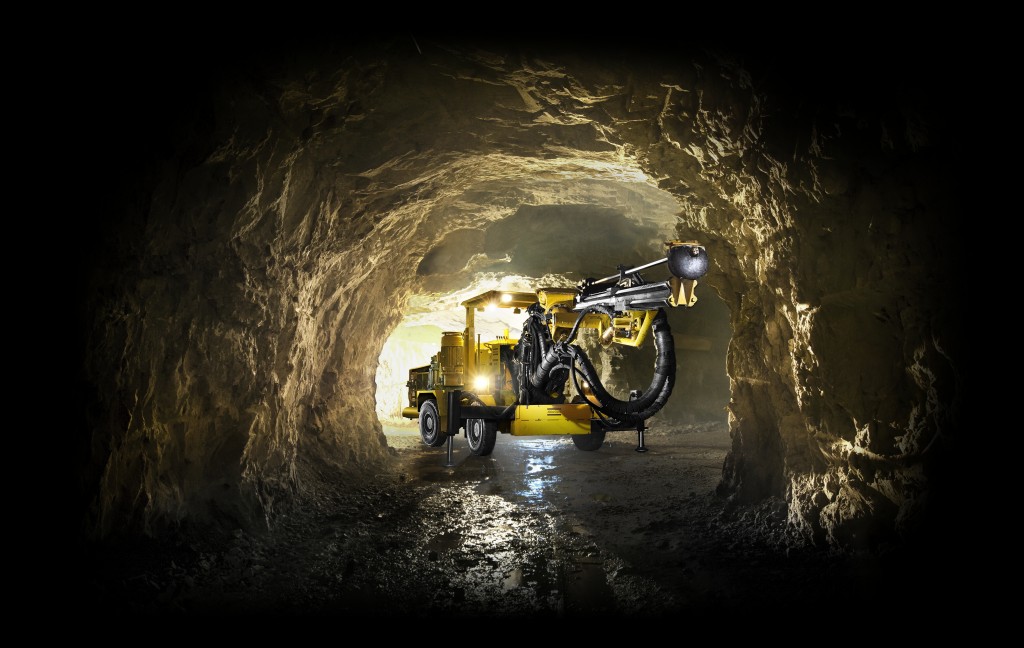
- Maquinaria común para barrenación de producción y avance:
Maquinas neumáticas, estas son perforadoras que utilizan como fuente de energía, aire comprimido (Requiriendo una presión entre 85 y 100 PSI, a menor de 70 PSI, será prácticamente imposible realizar barrenación sin dañar el equipo y los aceros, además de el extenso tiempo para barrenar, que pasa de un aproximado de 5 o 6 minutos por barreno hasta 15 o 20 minutos por cada barreno de 1.8 m) comúnmente en esta categoría, se utilizan las "Jackleg" o "Maquina de pierna", las cuales constan de:
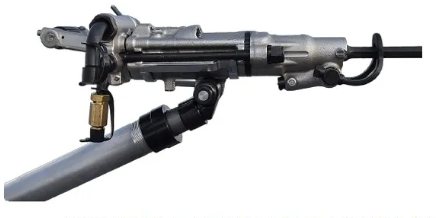
Broquero, siendo este el sitio donde se colocara el zanco de la barra, embonando así en la maquina, el cual es asegurado con el "Freno" evitando que la barra salga durante su utilización.
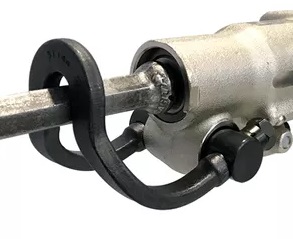
Aguja, este aditamento es el encargado de transmitir el agua a través del centro de la barra, la cual se utiliza para distintas funciones, tales como; Barrido rocoso del barreno, supresión de polvos y enfriamiento del acero, se debe revisar antes de su uso, pues es relativamente fácil de quebrarse.
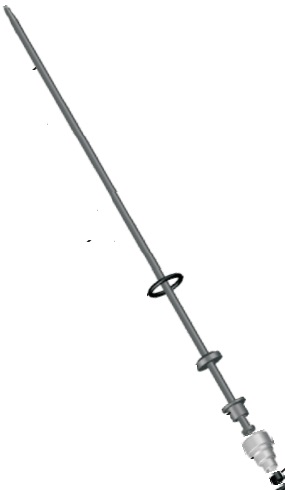
Piñón y manija de control, será con estas piezas con las cuales se controla el flujo de aire para dar la roto-percusión, además del ascenso y descenso del poste (Pierna)
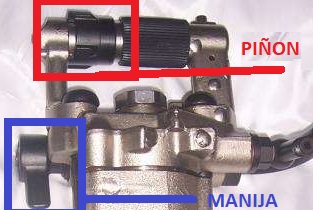
Conexiones (Spors), estas son las "Entradas" donde se conectaran las mangueras (Aire comprimido y agua), cabe mencionar que las mangueras se deben afianzar con "Ganchos" anti-whip que estén asegurados un extremo del spor y el otro de la manguera (Para en caso de que se suelte por alguna razón, no "chicotee" la manguera y así poder evitar accidentes), cabe mencionar que siempre hay que purgar bien las mangueras, pues en caso de traer contaminantes, pueden causar "Atascos" en la maquina, lo cual puede tener como desenlace daños en la maquina o hasta accidentes graves.
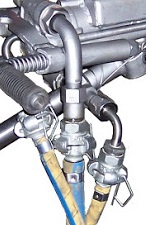
Poste (O pierna), este aditamento es el que es acoplado a la base de la perforadora (En la silleta y pivote), para que pueda soportarla, la pierna podrá ascender y descender (Dependiendo se requiera, será controlado en la manija), antes de empezar a realiza un barreno, deberá pisarse el "Apoyo" y fijarse firmemente al suelo con el "Torno de apoyo" (Este paso es fundamental, pues ante un "Atasco", esto evitara que se gire la pierna al "Ritmo" de la rotación, evitando así un accidente)
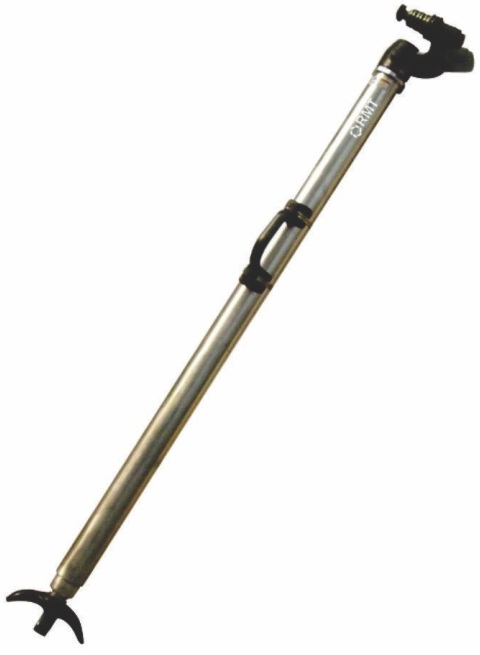
Lubricador (Tocho o rano), este aditamento, deberá conectarse en la línea del aire y ser llenado del aceite indicado, pues de esta forma "Viajara" a través de la línea hasta la maquina, el aceite requerido de manera vital para la lubricación durante el proceso de barrenación, evitando así daños mayores en el equipo.
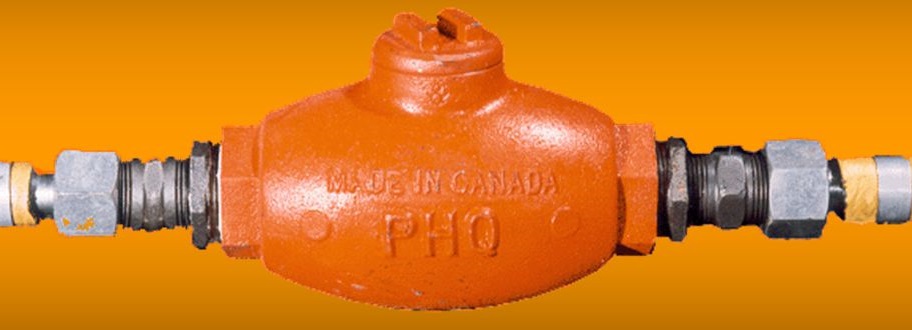
Maquinas electro-hidráulicas, existiendo de distintas maquinarias en marcas y modelos, pero en general mencionaremos la tan conocida palabra "Jumbo", los cuales son equipos mecánicos que tienen montada una perforadora (Pueden tener mas de una pluma), la cual funciona a Diesel para sus movimientos de traslado y eléctricamente para realizar la roto-percusión (Con corriente de 440 V), cabe mencionar que a diferencia de las maquinas neumáticas, no requiere aire comprimido, pues los movimientos de la pluma son realizados con fuerza hidráulica, gracias a la bomba hidráulica que es accionada con la corriente de 440 V.
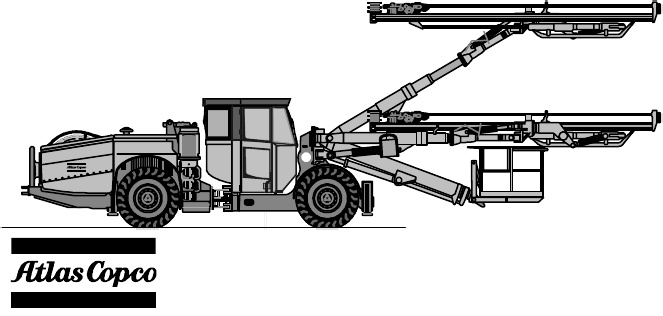
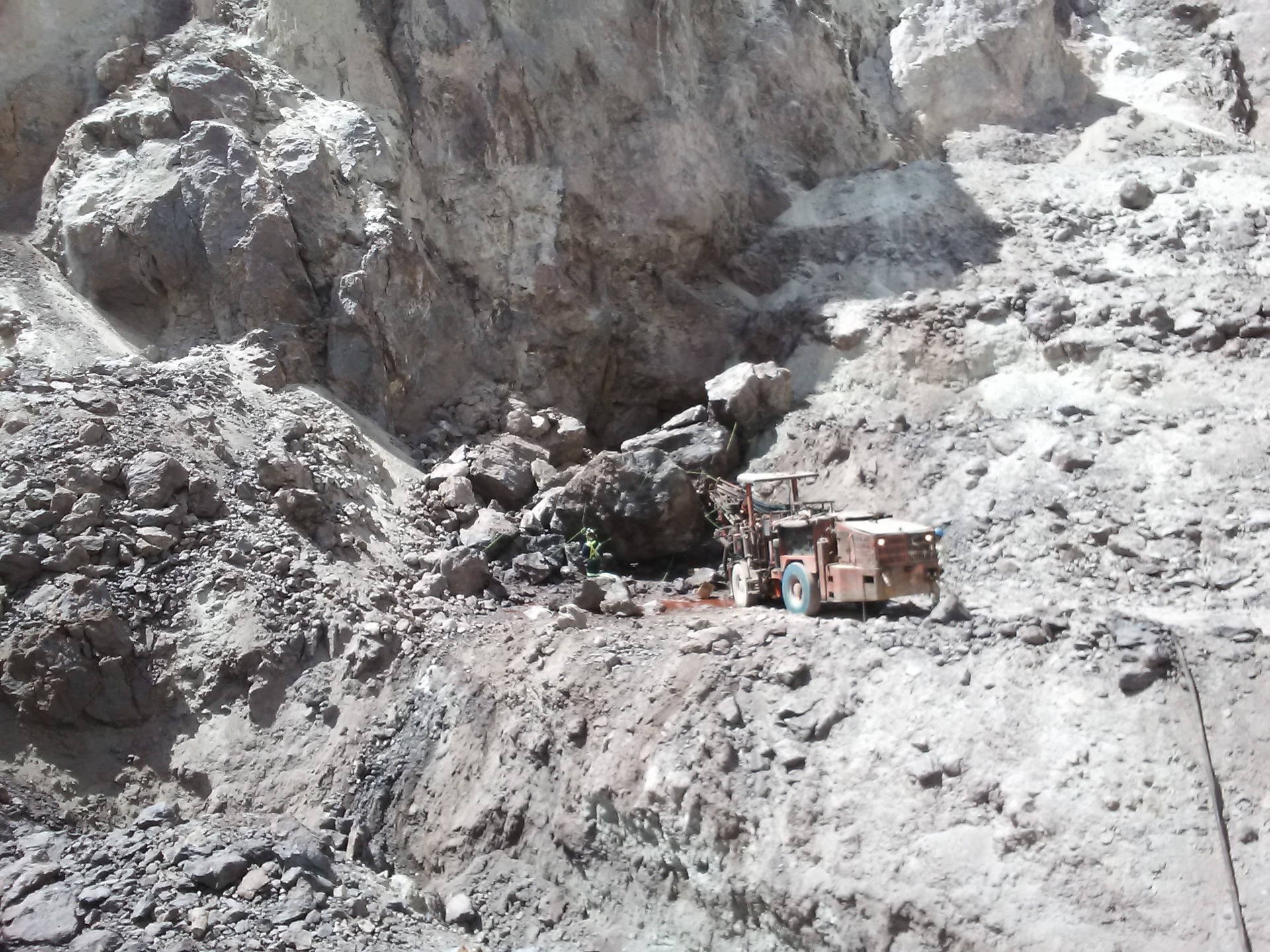
En el "Jumbo", tenemos dentro de la cabina un panel de control, donde existen tipos distintos de pantallas para notificar acerca de códigos de fallo en caso de presentar problemas de mantenimiento en lugares de sensores ubicados, además del lado contrario del volante para el control de la articulación (Que además se encuentra el encendido de motor Diesel, movimiento de elevación de canupi, pedales acelerador y freno, encendido de luces, etc.), se cuenta con la perforadora (En la parte de afuera), siendo de ese lado (Dentro de la cabina), donde están colocados los mandos para los distintos movimientos hidráulicos:
- Gatos de levante para posicionamiento del "Jumbo"
- Movimientos de avance y retroceso (Polea estacionaria y viajera)
- Movimiento telescópico
- Movimiento basculante
- Movimiento de giro de la viga de soporte de la perforadora
- Rotación
- Percusión
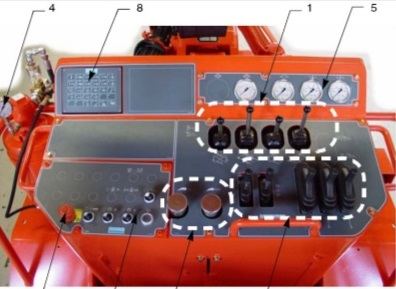
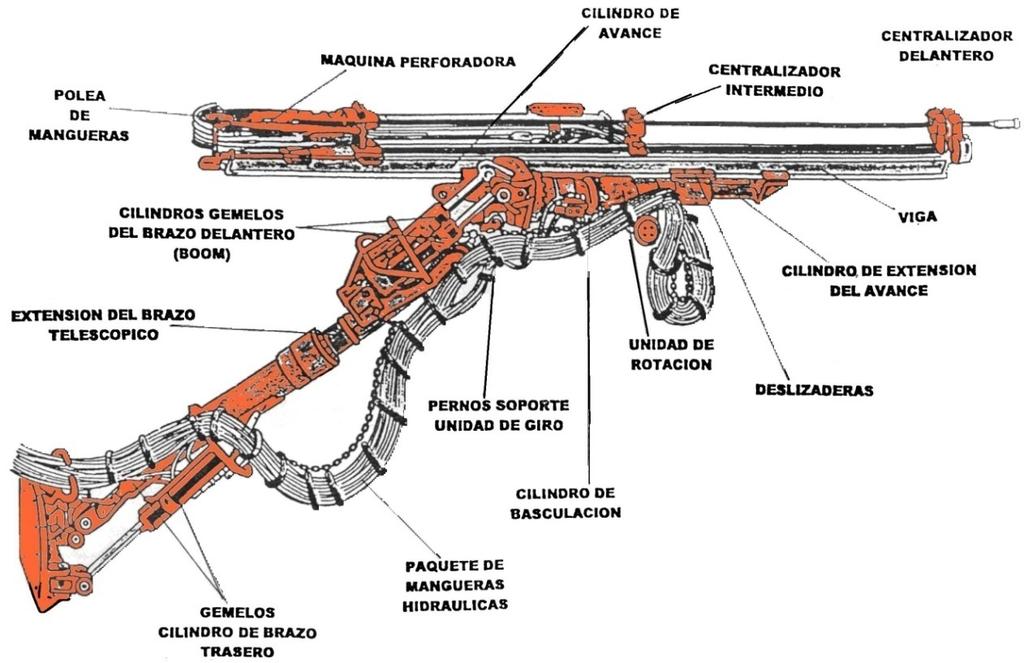
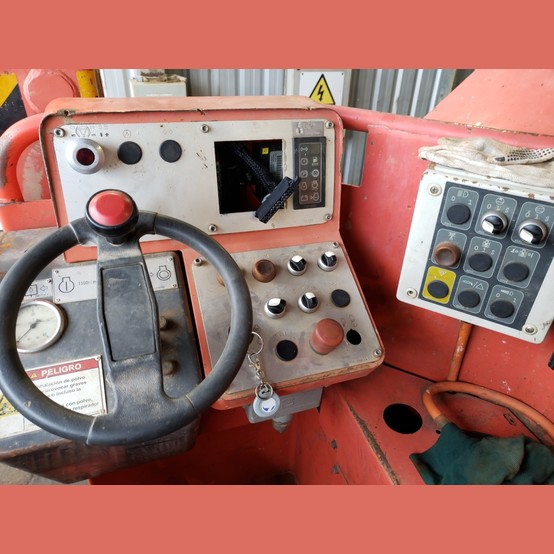
Además cabe mencionar que en la parte posterior del "Jumbo", se encuentran los paneles del motor eléctrico, donde se localizan:
- Switch principal, el cual es accionado luego de la conexión a la ploga, aseguramiento de sitio y de cable
- Se localizan los horómetros de compresor y de motor eléctrico (Sirven para la programación de mantenimiento)
- Conmutadores y relevadores
Este panel eléctrico no debe ser analizado por personal ajeno al encargado de mantenimiento eléctrico (Salvo para la prueba de aterrizado)
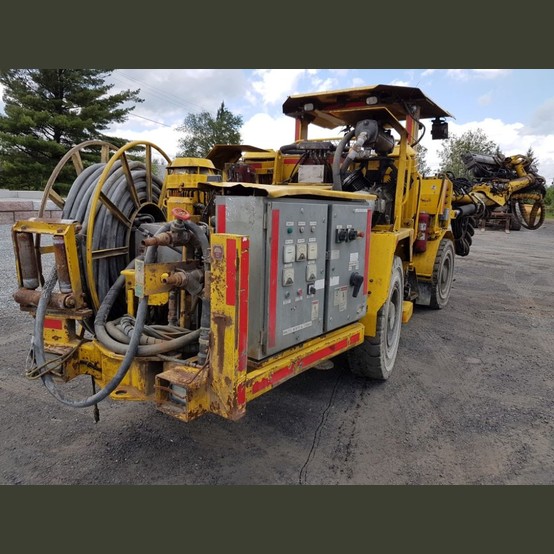
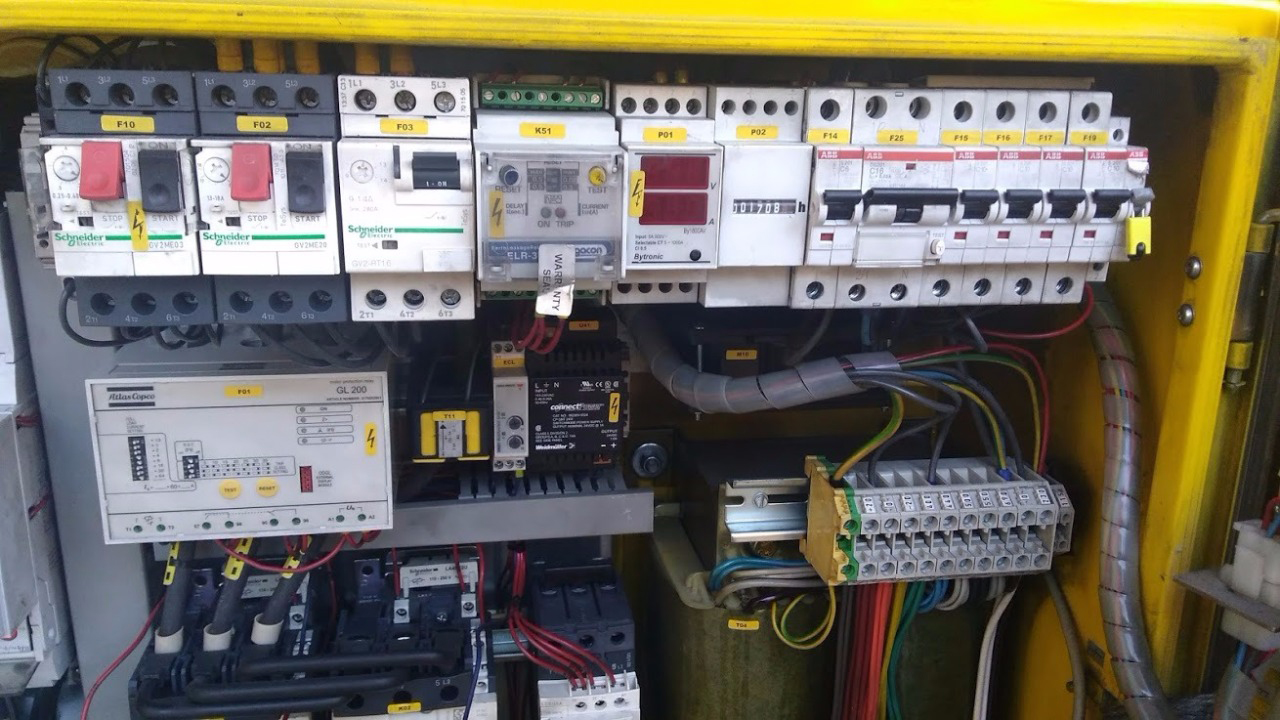
EN OTRA ENTRADA DE ESTE BLOG REVISAREMOS A MAYOR PROFUNDIDAD ESTE PASO "BARRENACIÓN"
- Cargado
En esta parte del ciclo, es de gran importancia que se asigne personal responsable y capacitado en el uso y manejo de explosivos así como se requiere que realice el cargado el jumbero con al menos un ayudante (El jumbero sabe como están los barrenos, cuales tienen problemas por lo quebrado, agua o algún otro parámetro "Problemático"), el o los ayudantes, tendrá que acercar la olla cargadora de ANFO cuando la barrenación este por concluir, teniendo conciencia de estabilidad del cielo y tablas del sitio donde sea colocada, además deberá alistar las mangueras que se requerirán, material como la pedacería de manguera antiestática o madera, para marcar los barrenos de piso, entre otros materiales requeridos, como la plancheta (De madera o aluminio) para el perforado de los bombillos para el cebado, faineros para el atacado de bombillos.
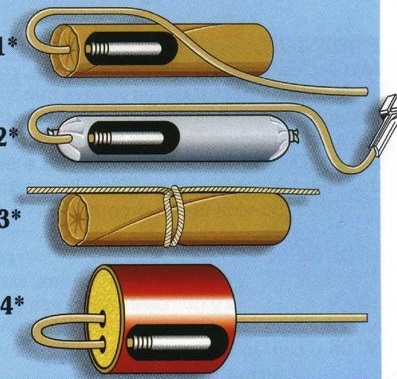
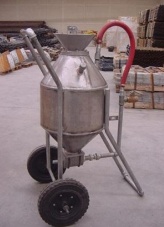
Tendrá que encargarse de tener condicionado los nichos o sitios donde se resguardara temporalmente el explosivo al momento de su arribo y antes de su uso.
Se requerirá una excelsa comunicación entre cargador y ayudante, pues aun portando el EPP adecuado para la tarea, por la falta de comunicación puede suceder accidentes en el manejo de los explosivos, aire comprimido y otros factores.
Durante el poblado y cargado de los barrenos, no deberá acercarse personal "No autorizado", pues es una actividad de "Alto riesgo".
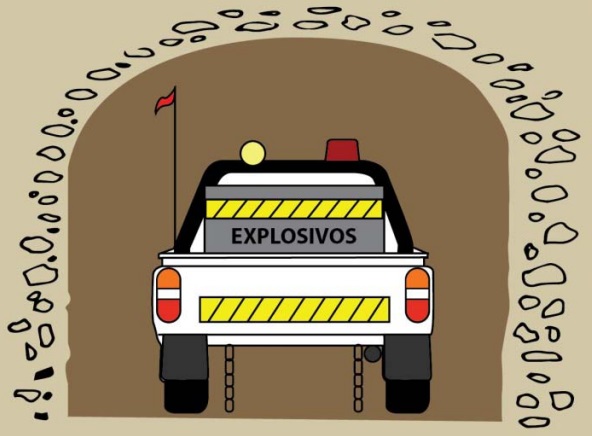
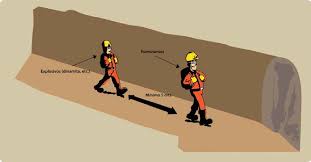
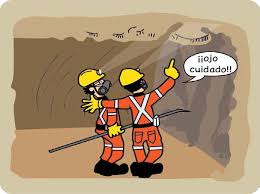
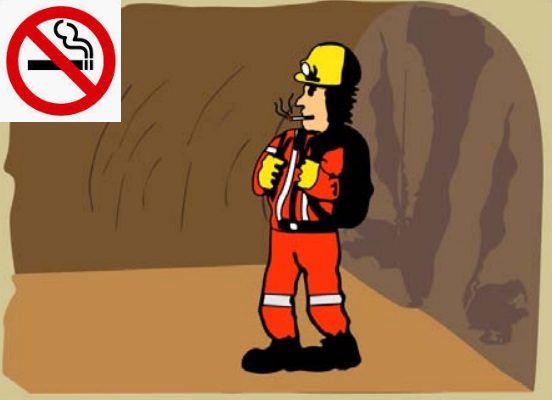
El cargado será el reflejo de la barrenación (Si esta mal barrenado, aun con buen cargado, se reflejaran los problemas técnicos), sin embargo, así también debe ser realizado por alguien con conocimiento de la colocación de explosivo (Alto y bajo), pues si la barrenación es buena, pero no se carga la adecuada columna o el fondo (Deficiente o en exceso), se obtendrá de resultado una mala voladura, sea en sobreexplotación o en perfiles inestables y/o excedentes (Patas, Tablas y cabeza).
Siempre debe ser colocada la plantilla con el orden de retardos como se requiere, siguiendo o generando "Cara libre" y siempre el resto de los retardos deben seguir el orden a la cara libre preexistente o recientemente generada.
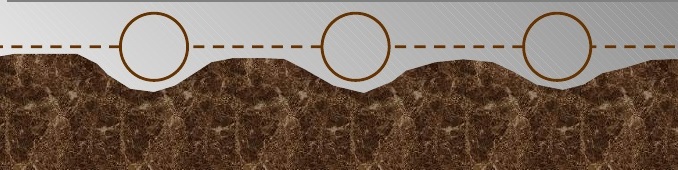
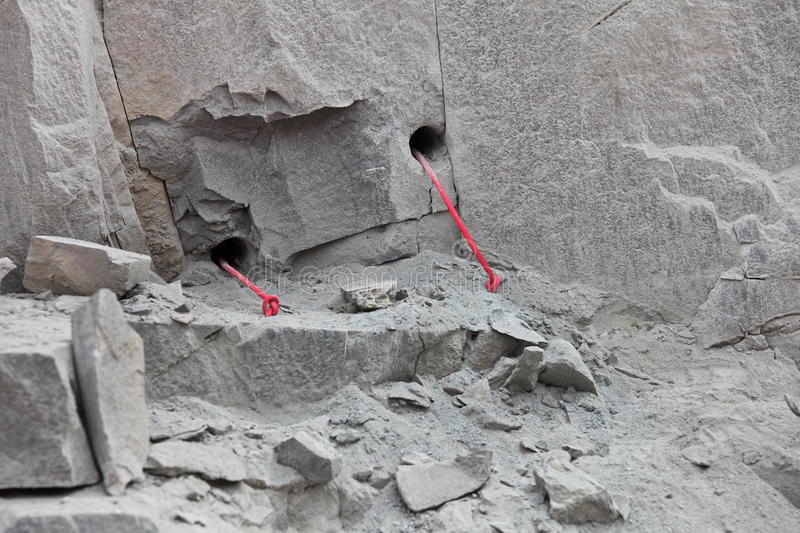
Ejemplos de obras que siguen cara libre
-Encapilles
-Cortes
-Bancos
Ejemplos de obras que deben generar cara libre
-Frente
-Tope
-Sill
Ejemplos de perfilados (Poseen cara libre comúnmente)
-Desborde
-Despate
-Descabece
Cabe mencionar, que al terminar el cargado, los retardos serán conectados al cordón detonante, mas sin embargo a este cordón, no se le amarrara aun la cañuela, hasta que estén totalmente listas el resto de las condiciones(Protocolo operativo, de tiempo y seguridad).
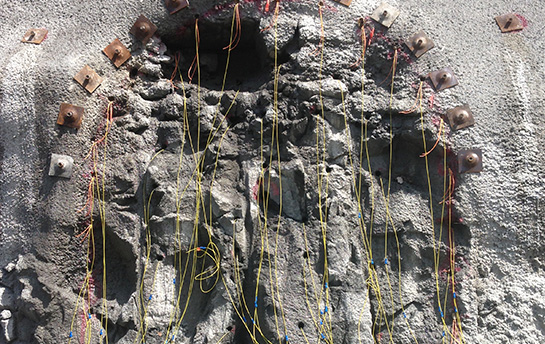
- Voladura
En este punto del ciclo, solamente cabe mencionar tres momentos del proceso:
- Antes de la voladura
Se debe iniciar el protocolo de voladura, lo primero es asegurar que se encuentre en el rango de horario de las voladuras, además que el área este libre de maquinaria, equipos y personal, que todo y todos deban estar completamente resguardados, que se coloquen guardas o guardias en los accesos, una vez asegurado todo lo anteriormente mencionado, el cargador y su ayudante, deberán amarrar a cañuela al cordón detonante, no deberá estar nadie mas en el área, mas que ellos (Y si fuese posible, el supervisor responsable), una ves listo todo, deberán arrimarle a la cañuela (En el arrimado -o encendido-, nunca debe estar una sola persona al realizarla, deberá haber al menos una persona mas, por motivos de seguridad).
Durante la voladura - Durante este evento, se deberá cumplir estrictamente un protocolo de seguridad, el cual debe incluir:
Personal vigilando accesos y/o guardas que informen acerca de la voladura en proceso (Además, si es posible la notificación vía radio, acerca del arrimado de la cañuela), se debe quedar personal en zonas seguras, hasta escuchar el disparo de la voladura (Solo con el fin de asegurar que suena completo el trueno con sus retardos correspondientes). - Luego de la voladura
Una vez realizada la voladura, deberá notificarse que ha sonado con éxito (O que ha fallado, según sea el caso), si no sonó completa, deberán tomarse las medidas de seguridad pertinentes (Lavados, tronar bombillos quedados, etc.), siempre respetando protocolos que aseguren la integridad del personal encargado de realizar las acciones.
Cabe mencionar que luego de la voladura, deberá encenderse los sistemas de ventilación, para asegurar que el área este ventilada correctamente para poder entrar al sitio a revisar,
Cuando se revise el área, se deberá hacer siempre portando el EPP adecuado, con detector de monódico y las medidas pertinentes para asegurar una entrada segura, siempre deberá prepararse el amacizaje para asegurar que no pasen accidentes debidos a las rocas sueltas en los perfiles de la obra.

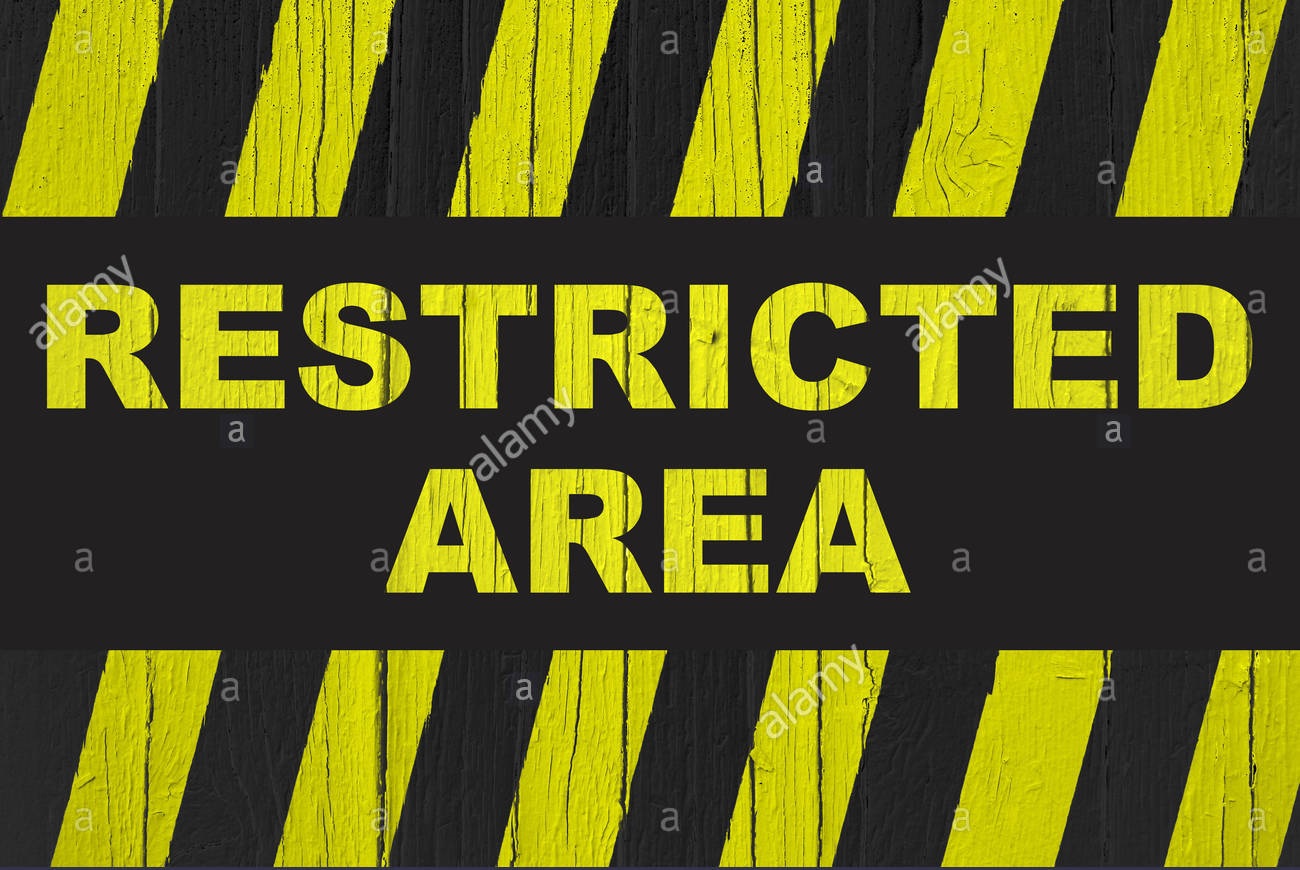
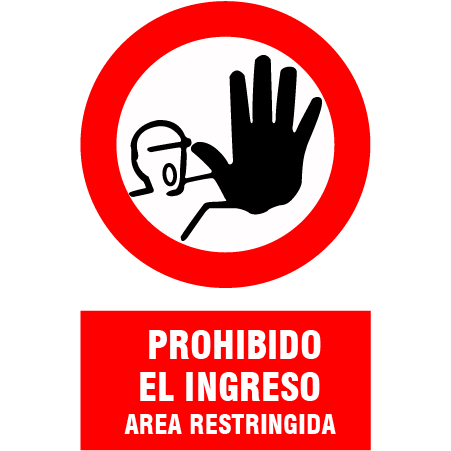
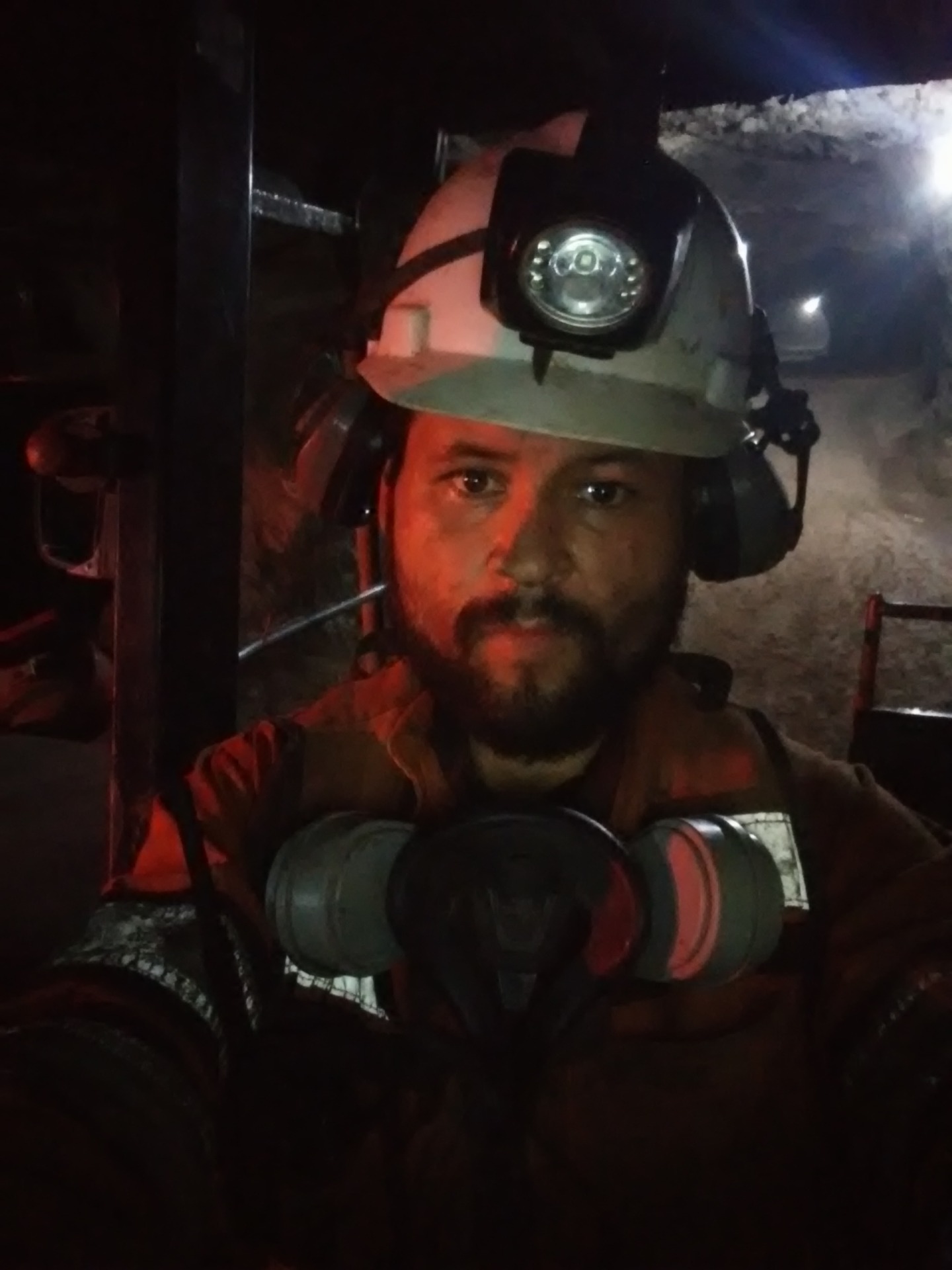
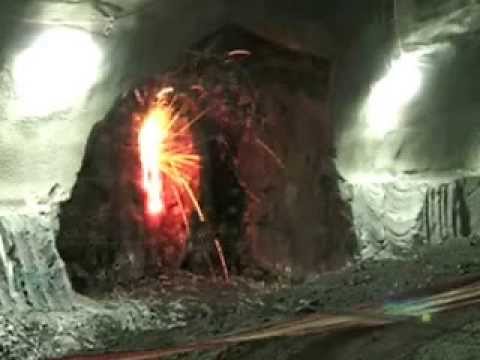
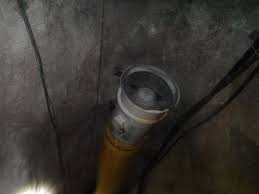
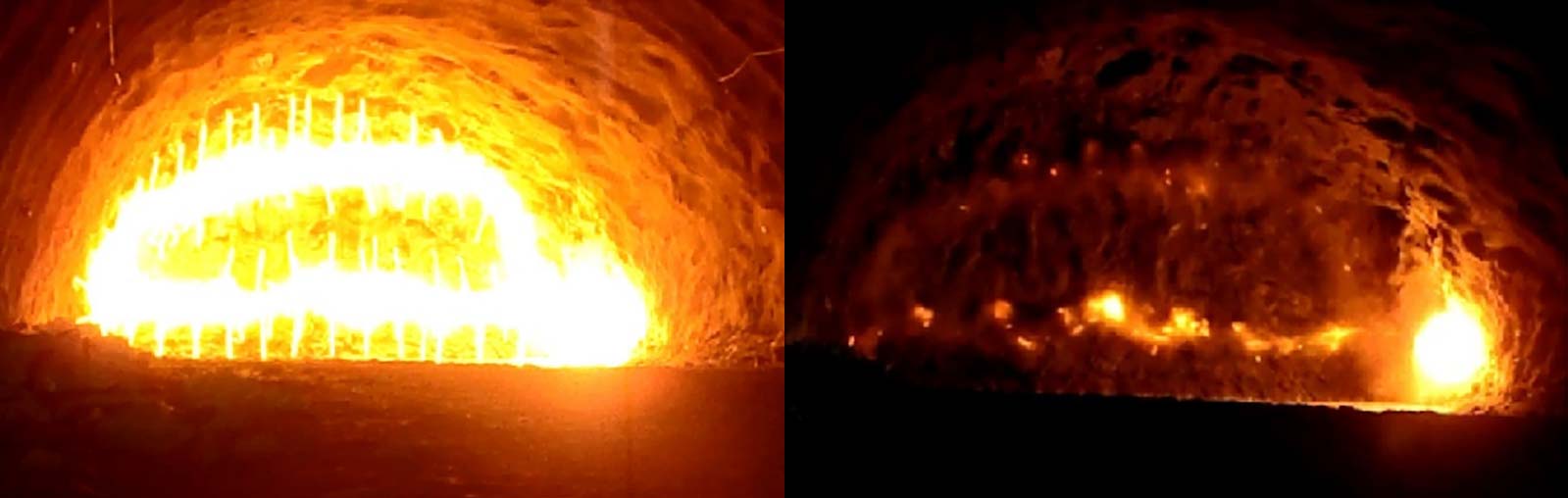
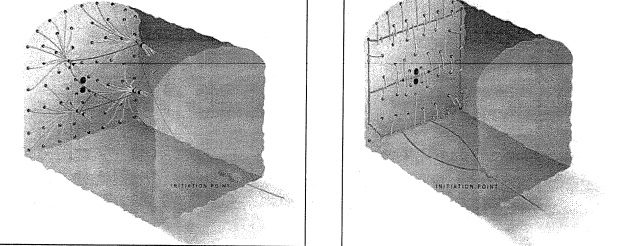
Siempre es importante priorizar la supervisión, pues esta actividad debe ser considerada vital para lograr el optimo desempeño debe ser exigida extrema y rigurosa seguridad antes, durante y después del evento de voladura
- Ventilación
Natural (Pudiendo ser en un rebaje -Por colar un ejemplo-), en este tipo de ventilación, el aire circulara por puros principios físicos de cambios de presión, por lo cual se limpiara el aire del área en un tiempo ya antes determinado, al momento de reingreso de personal en el área, se deberá asegurar el supervisor de operación o de ventilación, que el circuito no se encuentra viciado de gases nocivos para la salud.
Forzada (Pudiendo tratarse de topes o frentes ciegas, rampas, contra-rampas, etc.), en este tipo de ventilación, deberá asegurarse que este encendido el ventilador y que las mangas estén en orden (Antes del arrimado de la cañuela), si no existiera ventilador en el área, se puede asegurar la circulación del aire viciado en el circuito, con la línea de aire comprimido, para asegurar que en la obra se desplace el aire viciado por el fresco (Cabe mencionar como detalle importante, que el precio de la ventilación por línea de aire comprimido se eleva drásticamente en comparación con la ventilación por ventiladores, por lo cual, la línea de aire comprimido para realizar esta acción, debe ser utilizada solo como "Ultima instancia").
Todo esto es realizado con el afán de asegurar que pueda realizarse el ingreso en tiempo y forma adecuadas, evitando perdidas de tiempos innecesarios
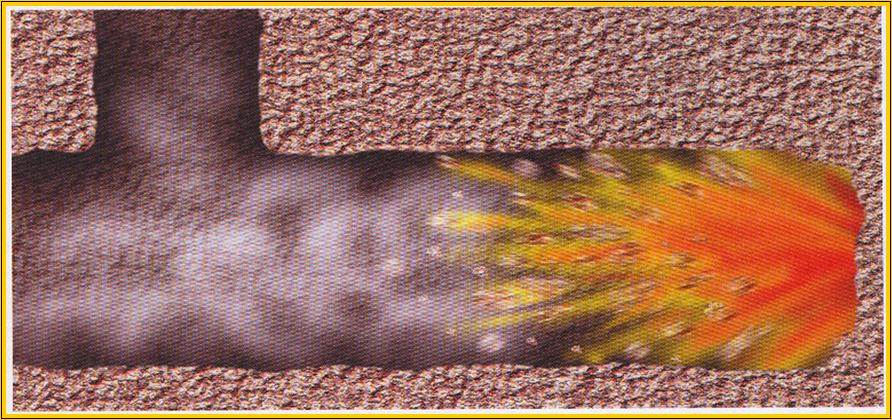

- Amacizaje
Este proceso consiste simplemente en realizar las acciones correspondientes y pertinentes para que las rocas que han quedado "Sueltas" o "Abiertas" luego de la fuerza de la detonación, sean desprendidas de cielo y tablas, para evitar que sucedan accidentes por descuido o complacencia al ingreso de personal en general, esta actividad puede ser realizada de dos maneras distintas (Realizando cualquiera de ellas o una "Combinación" de ambas):
Manual, esta "Técnica", consiste en la utilización de barras de amacizaje (Las cuales pueden ser de fierro -Barras condicionadas con punta y coa- o la mas adecuada para evitar lesiones en su uso, las de aluminio con punta de un lado y coa del lado contrario), este tipo de amacizaje consiste en la búsqueda de rocas "Abiertas", para utilizar la coa y así apalancar y facilitar la caída del material "Suelto" en los perfiles, la punta se utilizara para concentrar el esfuerzo en dicha punta, para generar "Fracturas" en las rocas que se escuchan "Bofas" o huecas y así conseguir generar esos puntos necesarios para que con la coa pueda soltarse la roca.
Es importante mencionar que debe mantenerse en lo mas cercano a un ángulo de 45°, además que la longitud de la barra debe sobrepasar al cuerpo (Pues si es mas corta, puede chicotear en alguna parte del cuerpo, en la caída de una roca, incluso hasta enterrarse en el cuerpo del trabajador, pudiendo desenlazarse de una manera fatal), esta actividad debe ser realizada con al menos un par de personas (Uno amacizando con la barra y el otro aluzando y estando de "Vigía" para evitar accidentes), en este proceso es de suma importancia realizar acorde a los procedimientos seguros de trabajo de la actividad, para evitar al máximo un resultado negativo en esta actividad (Ineficaz o accidentes).
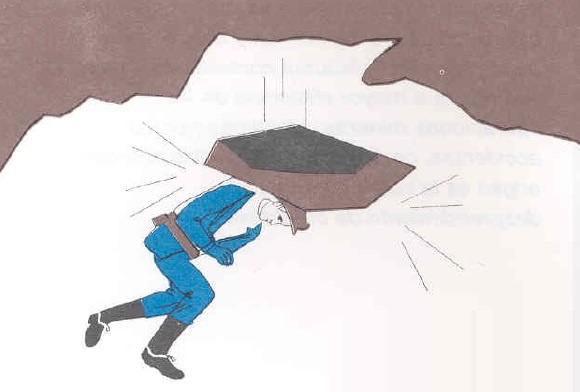
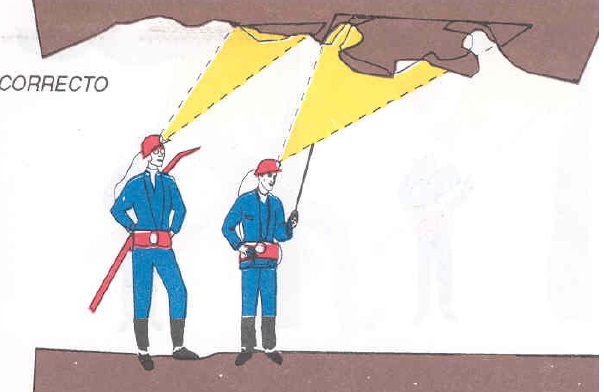
Mecanizado, la diferencia con la "Técnica" anterior, es que en esta manera de realizar el amacizaje, no se utilizan barras manuales de amacizaje, aquí se utiliza un equipo llamado "Scaler" o amacizador, el cual consiste en un martillo hidráulico montado en un chasis diésel, el cual cuenta con una pluma hidráulica, la cual es manipulada para alcanzar los distintos puntos de la obra minera, las principales ventajas de este método, es la disminución a la exposición a caídos al personal, además de la mayor eficiencia en tumbe y por ultimo se debe mencionar en la optimización de tiempo (Pues en sitios "Altos", no se espera a la realización de plantillas para el alcance de las barras manuales)
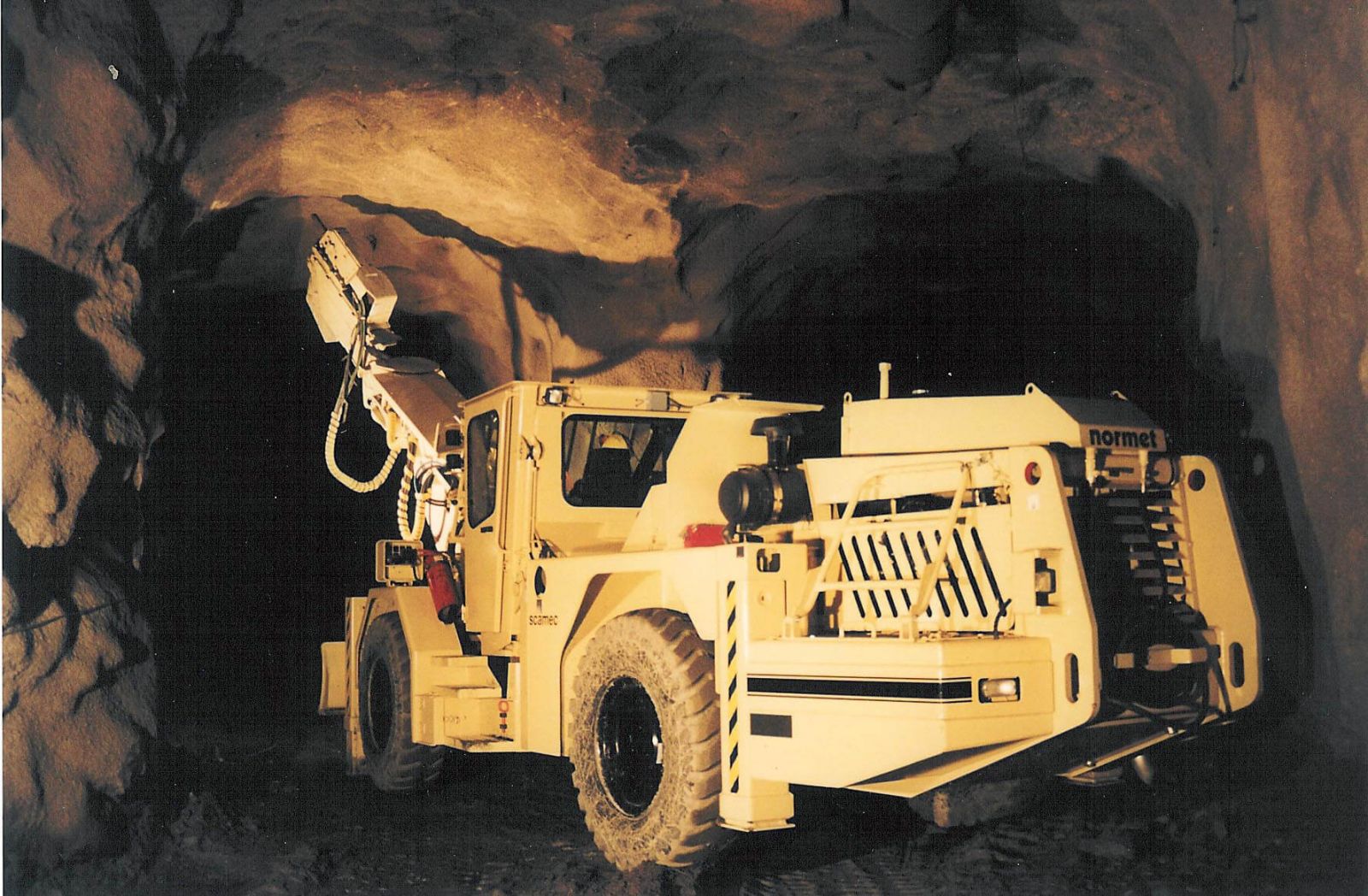
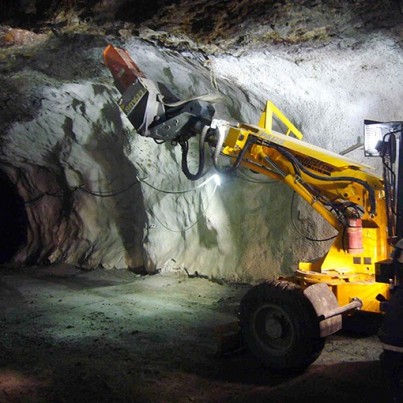
Cabe mencionar que este procedimiento debe ser realizado siempre de la zona segura hacia la insegura (De entrada a tope) y de cielo a tablas.
- Rezagado y acarreo
En este punto, se utiliza maquinaria pesada especializada para realizar la "Limpieza" de las áreas donde se realizo la voladura previamente, así mismo, transportar ese material (Esteria o de valor) al área correspondiente.
Rezagado, es la acción del movimiento del material utilizando un cargador de bajo perfil, el paleo o topeteo con aparato, la actividad de rezaga es fundamental para permitir el paso al siguiente punto, el cual puede ser la barrenación de nuevo (Reinicio de ciclo) o en caso de ser un área relativamente incompetente se procede al soporte o fortificación, si es un área que se requiere "Frenar" el intemperísmo (Ya sea por material arcilloso, disgregado o brechado), se realizara el zarpeo, enmallado y/o cerchado (Según sea requerido), para el paleo, existen dos tipos de material que se pueden movilizar.
Material de valor, este material es paleado del tope (Con Scooptram, escrepas, etc.), para ser enviado a stocks o a camiones de bajo perfil de acarreo, listo para el siguiente paso de su proceso.
Material estéril, este tipo de material (Que abunda, pues es el principal en obras de avance), es típicamente enviado a stocks tepetateros o a rellenos directamente, para continuar el ciclo de vida de minado de obras.
Cabe mencionar que el operador de Scooptram, deberá bajar del aparato al llegar al área poblada, pues deberá asegurarse que en el área existen condiciones "Seguras" para desempeñar su actividad planeada, en caso que se requiera amacizaje o algún tipo de actividad agregada a la actividad unitaria de rezagado (Algo no contemplado), deberá reportar inmediatamente, para que sea condicionado el sitio (Comúnmente debe participar el operador también, pero esto dependerá de la supervisión, pues posiblemente sea llevado a otra área, si el condicionamiento será muy tardado -Para aprovechar eficientemente el tiempo de funcionamiento del equipo-), así también, el operador deberá revisar en el área, para asegurar que no exista ningún tipo de equipo o material en el área de traslado del aparato, pues debe encargarse de garantizar la integridad de los materiales con los que se cuenta en el área(Ollas, barras, mangueras, mangas, etc.), el aperador además, deberá indicar en la entrada al área con distintos tipos de señalamientos (Letreros, bengalas, cinta, etc.) que se esta realizando actividad de rezagado en el interior del área y así evitar accidentes por la intromisión al área, por parte de personal no autorizado.
Acarreo, es la actividad unitaria en la cual gracias al cargador de bajo perfil, el camión de bajo perfil (Tipo Dompe), es cargado, para poder llevar el material de valor o estéril al área designada (Sea stocks, rellenos, plantillas, preparación mecánica, manteo, superficie, etc.)
- Soporte
Este punto se refiere a uno de los riesgos latentes mas importantes, el cual es la caída de rocas, la cual se debe considerar siempre que extraemos volúmenes del macizo rocoso (Alteramos el equilibrio natural de los sitios), aunado al movimiento turno a turno (Equipos generando gases y calor, energía de los explosivos, intemperísmo, ventilación, presencia de agua, etc.), por lo cual, para lograr mantener estables las obras mineras, se debe realizar actividades que disminuyan el riesgo de los peligro latente de los "Caídos", al realizar las acciones de soporte, combatiremos las condiciones negativas tales como la baja calidad de roca, zonas de altamente disgregado (Lo cual puede generar "Abocardamiento" descontrolado y posterior colapso de las obras), zonas de estratos demasiado fracturados, etc.
Debemos observar el terreno, así identificaremos las áreas que requieran fortificación, el factor principal que debemos monitorear es al desplazamiento de fallas, cuñas, el ensanchamiento de fracturas, etc.
Existen distintos tipos de soporte, los cuales deberán ser seleccionados con distintos factores (Tales como el tipo de obra -Permanente o temporal-, tipo de problema encontrado en el área -Falla, brecha, cucha, etc.-), los métodos principales se catalogan en:
-Pasivo, la cual al momento de la instalación, no realiza soporte de cargas, iniciara a soportar conforme el cerro "Trabaje" (Vaya cediendo o "Reposando"):
Arcos cedentes, estos tienden a ser de acero (Pero pueden ser de madera), la ventaja que tienen sobre los de madera, es que soportan mayor tonelaje, pero la desventaja que tiende a tener, es que al momento de falla, puede tronar sin aviso previo, aso contrario a la madera, la cual si truena periódicamente conforme va "Fallando", razón por la cual tienden a ponerse cuartones o calzas de madera sobre el arco y bajo el cielo y tablas de la obra minera, para que el cerro "Repose" sobre la cama de madera y pueda tener señales de fractura o sonoras conforme se aproxime el fallo del soporte.
Activo, este tipo de soporte es llamado así pues desde el momento de la instalación comienza a soportar esfuerzos del macizo rocoso, por lo cual, este tipo de soporto busca reestablecer el equilibrio de esfuerzos en el área ya alterada, su objetivo es convertir a la roca en "Autosoportable", pues no descansara el macizo sobre arcos o madera como en el caso anterior, sino que se mantendrá "In-situ":
Anclas, existen de distintos tipos, Split-set, de perno, de cable, de inyección de concreto, etc. estas anclas tienen distintas capacidades nominales de carga, cada una se utilizara en distintos casos (Ahondaremos en el tema en otra entrada), cabe mencionar que la instalación teórica o ideal, seria formando una herradura a lo largo del perfil de la obra, sin embargo, sabemos que en la mina no siempre se tienen condiciones ideales, por lo cual se buscara que estas anclas estén colocadas en forma perpendicular a los estratos, esto con el fin de lograr "Adherir" los estratos inestables a los que se encuentren mas estables en interior al macizo (Esto será mejor explicado en otra de las entradas)
Enmallado y concreto lanzado (Shortcrete), este tipo de sostenimiento se clasifica dentro del "Activo" por la razón que al momento de ser instalado y lanzado, ya comienza a soportar esfuerzos de caída y soporte rocoso, empieza a interferir contra el intemperísmo y evitar que las fallas o brechas se disgregue, una importante consideración en este tipo de soporte, es la humedad, el concreto lanzado no cumplirá su función de soportar si en este sitio existe alta filtración de agua.
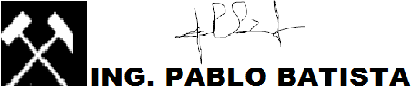